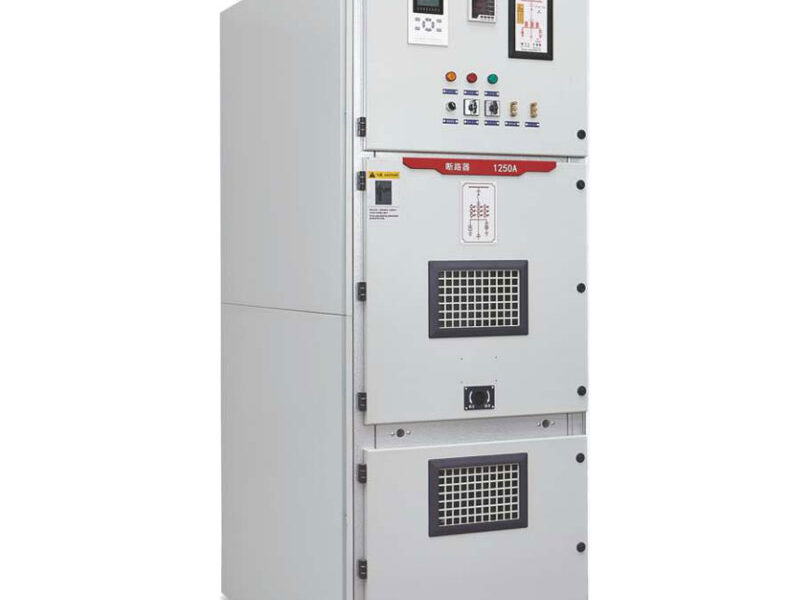
KYN28 High Voltage Switchgear Factory Test Process and Technical Key Points
1. Introduction
KYN28 high voltage switchgear is widely used in 12kV and 40.5kV medium voltage power distribution systems, primarily in power plants, substations, industrial enterprises, and infrastructure. As a core power distribution device, it plays a crucial role in controlling, protecting, and distributing electrical energy. Its operational reliability is directly related to the safety and stability of the power grid.
To ensure that KYN28 switchgear meets national standards (GB 3906, IEC 62271-200) and customer requirements, it must undergo strict testing before leaving the factory. This article provides a detailed overview of the factory test procedures, key technical parameters, and post-test handling to ensure optimal product performance.
2. Importance of Factory Testing for KYN28 High Voltage Switchgear
The primary goal of factory testing is to verify product quality, ensure user safety, and eliminate potential hazards. The main objectives include:
- Ensuring compliance with national and industry standards, such as GB 3906 and IEC 62271-200.
- Enhancing equipment reliability by identifying and correcting manufacturing defects to ensure long-term stable operation.
- Protecting the power system by preventing insulation failures, poor connections, or mechanical faults that could lead to short circuits, equipment damage, or grid failures.
- Reducing maintenance costs by detecting defects before delivery, minimizing repairs and downtime for users.
- Extending product lifespan by ensuring stable mechanical and electrical performance for long-term operation.
3. Factory Test Procedures and Key Technical Points for KYN28 Switchgear
Factory testing for KYN28 high voltage switchgear generally includes appearance inspection, mechanical performance tests, insulation tests, main circuit tests, secondary circuit inspection, switch performance tests, and safety protection tests.
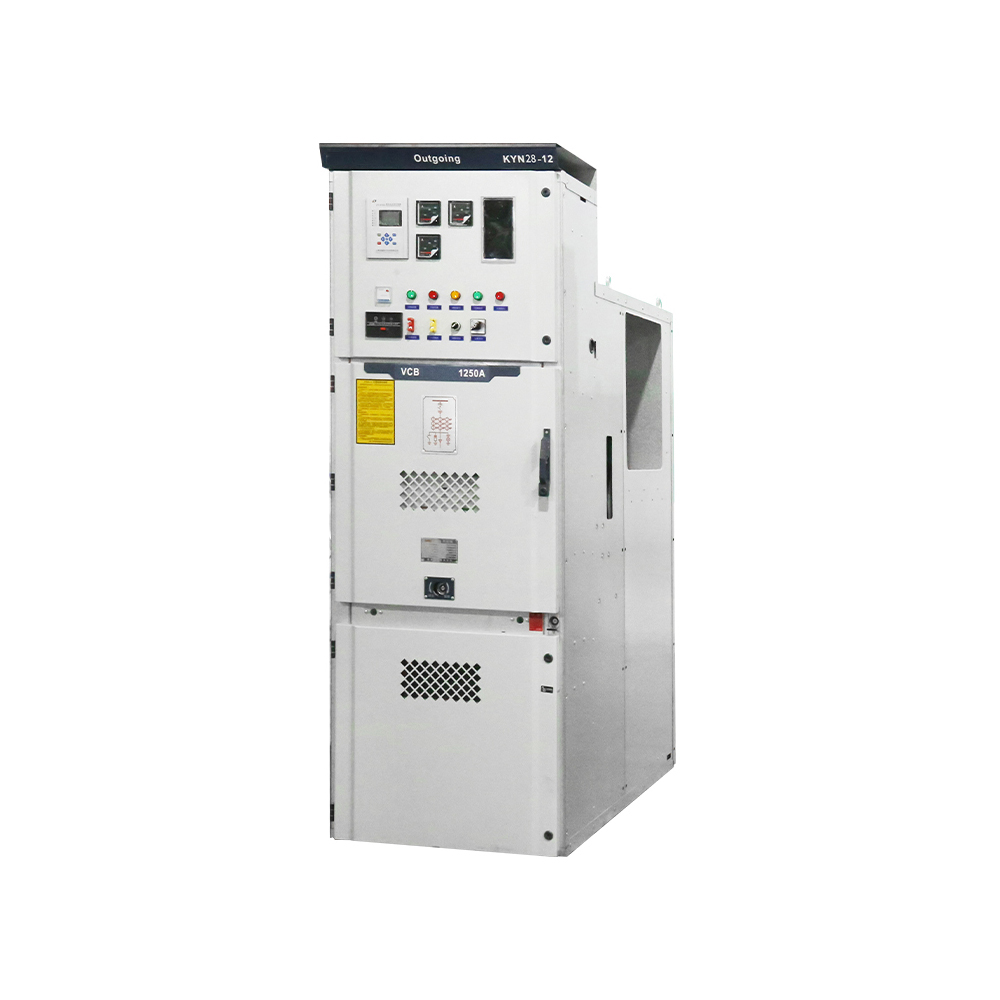
1. Appearance and Structural Inspection
Objective: Ensure the equipment has no visual defects and that mechanical components operate correctly.
Test Items:
- Cabinet structure inspection:
- The paint coating should be uniform, with no scratches, rust, or deformation of metal parts.
- Nameplate and labeling:
- The model, specifications, rated parameters, and manufacturing date must be clearly labeled.
- Terminal labels must be correct, and safety warning signs should be complete.
- Mechanical structure inspection:
- The circuit breaker handcart should move in and out smoothly without jamming.
- Closing and tripping operations must be smooth and reliable.
- Secondary circuit wiring should be neat, with no incorrect or loose connections.
- Interlocking device inspection:
- Five-proof (anti-misoperation) function test to prevent mis-closing, mis-opening, and unintended handcart movements.
-
KYN28-24 Metal-claded withdrawable AC metal-enclosed switchgear
2. Insulation Performance Tests
Objective: Verify the insulation capability of the KYN28 switchgear to prevent insulation breakdown or excessive leakage current.
Test Items:
- Insulation resistance test (using a 1000V/2500V megohmmeter)
- Main circuit phase-to-phase and phase-to-ground insulation resistance ≥1000MΩ.
- Secondary circuit insulation resistance ≥10MΩ.
- Power frequency withstand voltage test (most critical)
- 12kV switchgear: Apply 42kV for 1 minute; no flashover or breakdown should occur.
- 35kV switchgear: Apply 80kV for 1 minute.
- Secondary circuit withstand voltage test: Apply 2kV for 1 minute to ensure insulation capability of protection and control circuits.
- Partial discharge test (for GIS or high-insulation-grade cabinets)
- Apply high voltage and measure partial discharge levels, ensuring ≤10pC (standard requirement).
3. Main Circuit Conductivity Test
Objective: Ensure that the main circuit has low resistance, preventing overheating and energy loss due to poor connections.
Test Items:
- Circuit resistance test (using a 100A DC micro-ohmmeter)
- The resistance at busbar connections and circuit breaker contacts should be ≤200μΩ.
- Temperature rise test (sampled test)
- Run at rated current and measure temperature rise at busbars and connection points to ensure no overheating during long-term operation.
4. Secondary Circuit Inspection and Functional Tests
Objective: Ensure that protection, measurement, control, and communication functions operate correctly.
Test Items:
- Secondary circuit wiring check
- Verify wiring against drawings, ensuring correct connections and firm terminals.
- Protection relay testing
- Conduct overcurrent, short circuit, undervoltage, and instantaneous trip protection tests to ensure response times meet set values.
- Remote and local operation tests
- Verify SCADA/remote control and local operation functions, ensuring correct switching and signal feedback.
- CT/PT ratio and polarity test
- Use a transformer ratio tester to verify secondary output accuracy and correct polarity.
5. Circuit Breaker and Load Switch Performance Tests
Objective: Ensure that switching devices operate reliably and meet timing requirements.
Test Items:
- Opening and closing time measurement (using a circuit breaker analyzer)
- Circuit breaker closing time ≤60ms, opening time ≤50ms.
- Mechanical characteristic test
- Contact bounce time should be ≤2ms, ensuring no abnormal vibrations.
- Repeated switching operation reliability test
- Perform 20-50 consecutive open/close operations to verify the durability of the mechanism.
6. Safety Protection and Grounding Inspection
Objective: Ensure the switchgear’s protective performance to prevent external environmental impacts on operation.
Test Items:
- IP protection level check (such as IP4X, IP54).
- Grounding continuity test
- The cabinet grounding resistance should be ≤0.1Ω, ensuring a reliable connection to the grounding system and preventing leakage current hazards.
4. Post-Test Handling and Summary
- After completing all tests, a full test report must be generated and signed by quality inspectors for record-keeping.
- If any issues are found during testing, troubleshooting must be performed, and retesting must be conducted until the product passes.
- Only products that pass all tests can receive a “qualified” label, a factory acceptance certificate, and be delivered to customers.
5. Conclusion
The factory testing of KYN28 high voltage switchgear is a critical quality control step. By strictly following procedures for appearance inspection, insulation tests, conductivity tests, secondary circuit function checks, and switchgear performance tests, manufacturers can effectively eliminate product defects, improve safety and reliability, and ensure stable power grid operation. Strict adherence to standardized testing processes is essential to delivering high-quality, safe, and reliable switchgear to customers.